The Role of CNC Machining in Modern Manufacturing
CNC machining has transformed modern manufacturing, moving beyond traditional manual processes to become a cornerstone of efficient, precise production. Short for "computer numerical control machining," CNC machining uses computer programs to control machine tools—such as mills, lathes, and routers—enabling automated, consistent, and complex part production. In an era where manufacturers demand speed, accuracy, and flexibility, CNC machining delivers on all fronts, supporting industries from automotive to aerospace and medical devices. Let’s explore its critical role in modern manufacturing.
Precision and Consistency: The Foundation of Quality
One of the most vital roles of CNC machining in modern manufacturing is delivering unmatched precision and consistency—qualities that are non-negotiable for today’s high-performance products.
Traditional manual machining relies on human skill, which can lead to small errors in measurements. Even the most experienced machinists may produce parts with slight variations, especially when working on complex designs. CNC machining eliminates this variability. By following preprogrammed computer codes, CNC machines can repeat the same cuts and movements to within 0.0001 inches (2.5 microns) of accuracy. This level of precision ensures that every part produced is identical, whether it’s the first or the 10,000th in a batch.
This consistency is critical for industries like aerospace, where a single mismatched part in an aircraft engine could lead to catastrophic failure. In medical manufacturing, CNC machining produces precise components for surgical tools and implants (e.g., knee replacements), ensuring they fit perfectly with the human body. Modern manufacturing’s focus on quality and safety makes CNC machining indispensable—it’s the gold standard for parts that must perform reliably under extreme conditions.
Efficiency and Productivity: Speeding Up Production
Modern manufacturing demands faster turnaround times, and CNC machining plays a key role in boosting efficiency and productivity.
CNC machining reduces production time in several ways:
- Automation: Once programmed, CNC machines can run 24/7 with minimal human intervention. This means manufacturers can produce parts overnight or during weekends, significantly increasing output compared to manual machining, which stops when workers go home.
- Reduced setup time: Switching between different parts in CNC machining is faster than with traditional tools. Operators simply load a new program and material, rather than reconfiguring entire workstations. This makes CNC machining ideal for both large-scale production runs and small batches.
- Less waste: CNC machining cuts materials with pinpoint accuracy, reducing scrap. For example, a CNC lathe can shape a metal rod into a part with 95% material utilization, compared to 70% with manual turning. Less waste lowers costs and supports sustainability goals in modern manufacturing.
A study by the Manufacturing Technology Association found that CNC machining can increase production speed by 50–300% compared to manual methods, a game-changer for meeting tight deadlines in competitive markets.
Flexibility and Adaptability: Meeting Changing Demands
Modern manufacturing is no longer just about mass production—it’s about adapting to changing consumer demands, including smaller batches, custom designs, and rapid product updates. CNC machining excels at this flexibility.
Unlike traditional machines, which are often built for one specific task (e.g., a manual lathe for making bolts), CNC machining centers are highly adaptable. With a simple program change, a single CNC machine can switch from making a gear one hour to a custom bracket the next. This versatility is critical for:
- Customization: Brands now offer personalized products, from engraved smartphone cases to custom-fit automotive parts. CNC machining makes this possible by quickly adjusting to unique designs without retooling.
- Prototyping: In product development, manufacturers need to test multiple prototypes. CNC machining can produce a single prototype in hours, allowing teams to iterate and improve designs faster than with traditional methods, which may take days or weeks.
- Short runs: For niche markets (e.g., specialized industrial tools), CNC machining efficiently handles small batches (10–100 parts) without the high costs of setting up dedicated production lines.
This flexibility helps modern manufacturers stay agile, responding to trends and customer needs without delays.
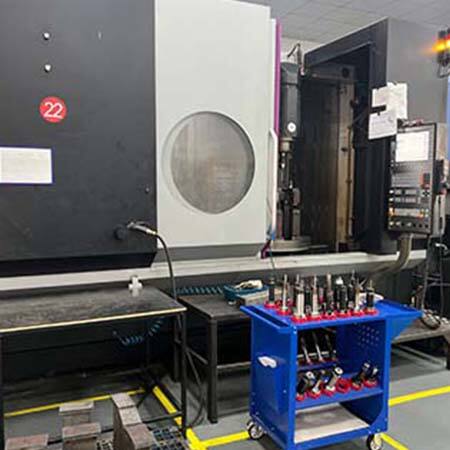
Enabling Advanced Materials and Complex Designs
Modern manufacturing increasingly uses advanced materials—such as high-strength alloys, composites, and heat-resistant plastics—that are difficult to shape with manual tools. CNC machining handles these materials with ease, expanding design possibilities.
- Hard metals: Titanium and Inconel, used in aerospace and energy industries, are too tough for manual machining. CNC machines with high-powered spindles and carbide tools can cut these materials accurately, creating parts like turbine blades and oil rig components.
- Composites: Carbon fiber composites, popular in automotive and sports equipment, require precise cutting to avoid fraying. CNC routers with specialized software ensure clean edges, maintaining the material’s strength.
- Complex geometries: Modern products often feature intricate designs—curved surfaces, internal channels, or 3D shapes—that manual machining can’t replicate. 5-axis CNC machining, which moves parts along five axes simultaneously, creates these complex forms in one setup, reducing errors and saving time.
Without CNC machining, many of today’s most innovative products—from lightweight electric vehicle parts to miniaturized medical devices—would be impossible to manufacture.
Integration with Smart Manufacturing Systems
Modern manufacturing is moving toward "smart factories," where machines, sensors, and software work together to optimize production. CNC machining is a key component of this integration, acting as a bridge between digital design and physical production.
- CAD/CAM integration: CNC machines work seamlessly with computer-aided design (CAD) and computer-aided manufacturing (CAM) software. Engineers design parts in CAD, and CAM software converts these designs into CNC programs, eliminating manual coding and reducing errors.
- Data collection: Smart CNC machines are equipped with sensors that track performance—cutting speed, tool wear, and energy use. This data is sent to manufacturing execution systems (MES), which identify bottlenecks and adjust production in real time. For example, if a sensor detects a dull tool, the system can alert operators to replace it before it ruins parts.
- Predictive maintenance: Using AI and machine learning, manufacturers analyze data from CNC machines to predict when maintenance is needed (e.g., spindle replacement). This prevents unexpected breakdowns, keeping production running smoothly.
By integrating with smart systems, CNC machining makes modern manufacturing more efficient, transparent, and responsive.
Industry-Specific Roles of CNC Machining
CNC machining plays unique roles across different sectors of modern manufacturing:
- Automotive: Produces engine parts, gears, and custom components for electric vehicles (EVs). CNC machining’s speed and precision support the high-volume production of EV batteries and motor parts.
- Medical: Creates surgical instruments, prosthetics, and implantable devices (e.g., pacemaker components) with strict tolerances, ensuring patient safety.
- Aerospace: Manufactures lightweight, high-strength parts for planes and rockets, such as wing brackets and fuel system components, where even small errors can be dangerous.
- Electronics: Produces precise parts for smartphones, computers, and circuit boards, including tiny connectors and heat sinks.
- Consumer goods: Makes custom furniture hardware, jewelry, and kitchen appliances, meeting demand for personalized and high-quality products.
In each industry, CNC machining’s ability to balance precision, speed, and flexibility makes it irreplaceable.
FAQ: CNC Machining in Modern Manufacturing
What is CNC machining, and how is it different from manual machining?
CNC machining uses computer programs to control machine tools, ensuring precise, consistent parts. Manual machining relies on human operators, which can lead to variations. CNC is faster, more accurate, and better for complex designs.
Why is CNC machining important for modern manufacturing?
It enables high precision, fast production, and flexibility to handle custom or small-batch orders—key needs in today’s market. It also works with advanced materials and integrates with smart factory systems.
Can CNC machining produce small parts?
Yes. CNC machines with high-resolution spindles can make tiny parts, such as microchips or medical device components, with dimensions as small as 0.001 inches.
How long does it take to program a CNC machine?
Simple parts take 30 minutes to an hour to program using CAD/CAM software. Complex designs may take a few hours, but once programmed, the machine can produce parts repeatedly without rework.
Is CNC machining environmentally friendly?
It’s more efficient than manual machining, reducing material waste and energy use. Many modern CNC machines use eco-friendly coolants and are designed to minimize emissions.
Will CNC machining replace human workers?
No, but it changes their roles. Workers now program machines, monitor production, and handle maintenance, focusing on skilled tasks rather than manual labor.
Table of Contents
- The Role of CNC Machining in Modern Manufacturing
- Precision and Consistency: The Foundation of Quality
- Efficiency and Productivity: Speeding Up Production
- Flexibility and Adaptability: Meeting Changing Demands
- Enabling Advanced Materials and Complex Designs
- Integration with Smart Manufacturing Systems
- Industry-Specific Roles of CNC Machining
-
FAQ: CNC Machining in Modern Manufacturing
- What is CNC machining, and how is it different from manual machining?
- Why is CNC machining important for modern manufacturing?
- Can CNC machining produce small parts?
- How long does it take to program a CNC machine?
- Is CNC machining environmentally friendly?
- Will CNC machining replace human workers?