How to Achieve High-Quality Custom CNC Machining Parts
Custom CNC machining has become a cornerstone of modern manufacturing, enabling the production of precise, complex parts for industries ranging from aerospace to medical devices. The key to success lies in delivering high-quality custom CNC machining parts—components that meet strict dimensions, surface finishes, and performance standards. Achieving this level of quality requires careful planning, attention to detail, and the right combination of materials, equipment, and processes. Let’s explore the essential steps to ensure your custom CNC machining parts are consistently high-quality.
Start with Material Selection for Custom CNC Machining
The foundation of high-quality custom CNC machining parts is choosing the right material. Different materials respond differently to machining, and selecting one that matches your part’s intended use and manufacturing requirements is critical.
Match Material to Part Function
- Metals: Aluminum, steel, and titanium are popular for custom CNC machining due to their strength and machinability. Aluminum (e.g., 6061) is lightweight and easy to machine, making it ideal for aerospace parts. Steel (e.g., 4140) offers durability for industrial components, while titanium is corrosion-resistant, perfect for medical implants.
- Plastics: Materials like ABS, PEEK, and nylon are used for custom CNC machining when weight, flexibility, or chemical resistance is needed. PEEK, for example, withstands high temperatures, making it suitable for automotive under-the-hood parts.
Always verify material certifications (e.g., ISO, ASTM) to ensure consistency. Low-quality or mismatched materials can lead to poor surface finishes, dimensional errors, or part failure during use.
Prepare Materials Properly
Before custom CNC machining, materials must be properly prepared:
- Cut to size: Use precision saws to cut raw materials into blanks (rough shapes) close to the final part size. This reduces machining time and minimizes tool wear.
- Remove defects: Inspect blanks for cracks, warping, or impurities. Even small flaws can worsen during machining, ruining the part.
- Heat treatment: For metals like steel, heat treatment (annealing, quenching) can reduce hardness, making them easier to machine and improving final part strength.
Proper material preparation sets the stage for smooth, accurate custom CNC machining.
Invest in Quality Equipment and Tooling for Custom CNC Machining
The accuracy of custom CNC machining parts depends heavily on the equipment and tools used. Outdated or poorly maintained machines can introduce errors, while high-quality tools ensure clean, precise cuts.
Choose the Right CNC Machine
CNC machines come in various types, including mills, lathes, and routers. Select one that matches your part’s complexity:
- 3-axis CNC mills: Suitable for simple 2D or 3D parts (e.g., brackets, plates).
- 5-axis CNC machines: Handle complex, multi-sided parts (e.g., aerospace components) with angles and curves, reducing the need for multiple setups.
Modern CNC machines with high-resolution controllers (0.0001-inch accuracy) are essential for tight tolerances. Look for machines with rigid frames to minimize vibration during custom CNC machining—vibration causes tool chatter, leading to rough surfaces and dimensional errors.
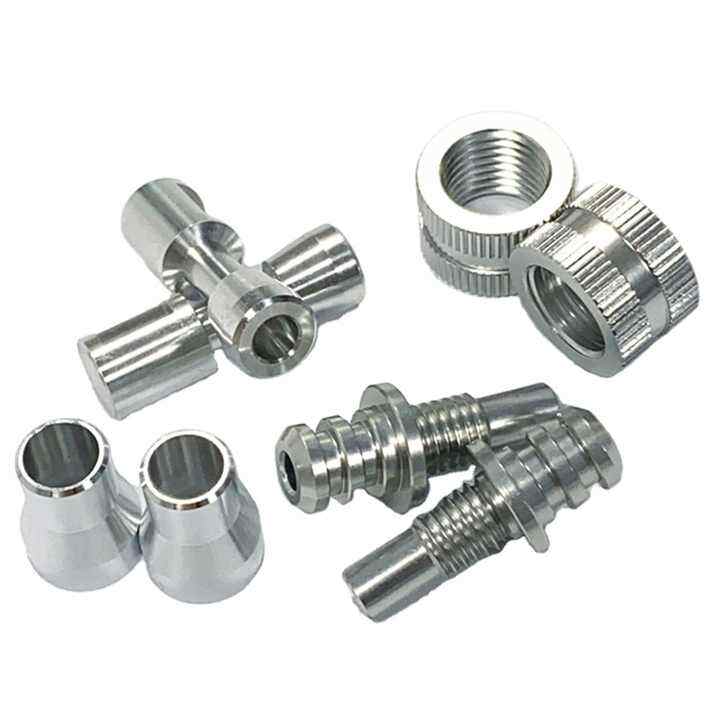
Use High-Quality Cutting Tools
Cutting tools (end mills, drills, inserts) directly impact custom CNC machining quality:
- Material: Carbide tools are harder and more heat-resistant than high-speed steel (HSS), lasting longer and producing smoother cuts. Ceramic tools work well for high-temperature alloys like Inconel.
- Coatings: Titanium nitride (TiN) or diamond coatings reduce friction and wear, extending tool life and improving surface finishes.
- Size and geometry: Match tool diameter and flute count to the material and cut type. For example, 4-flute end mills are better for finishing passes in custom CNC machining, while 2-flute tools remove material faster for roughing.
Regularly inspect tools for wear and replace them when dull—blunt tools force the machine to work harder, increasing errors and tool breakage risk.
Optimize Programming for Custom CNC Machining
CNC programming converts part designs into machine-readable code (G-code, M-code), dictating tool paths, speeds, and feeds. Poor programming is a leading cause of quality issues in custom CNC machining.
Focus on Tool Path Planning
- Avoid sharp turns: Sudden changes in direction can cause tool vibration. Use smooth, arc-based tool paths in custom CNC machining to maintain consistent cutting forces.
- Climb vs. conventional milling: Climb milling (tool rotates with the material) produces cleaner finishes but requires rigid setups. Conventional milling is safer for flexible materials but may leave marks.
- Layered cutting: For deep cuts, remove material in thin layers (0.01–0.05 inches per pass) instead of one deep cut. This reduces tool stress and improves accuracy.
Simulation software (e.g., Mastercam, Fusion 360) helps test tool paths before custom CNC machining, identifying collisions or inefficient paths that could damage the part or machine.
Set Optimal Speeds and Feeds
Speeds (tool rotation, RPM) and feeds (material removal rate, inches per minute) must be tailored to the material and tool:
- High speeds/low feeds: Work for plastics and soft metals (aluminum) to prevent melting or deformation.
- Low speeds/high feeds: Suitable for hard metals (titanium) to avoid overheating tools.
Most CNC software includes databases with recommended speeds and feeds for common materials, but adjust based on real-time feedback—listen for unusual noises (e.g., screeching) during custom CNC machining, which signal incorrect settings.
Ensure Accurate Fixturing and Workholding in Custom CNC Machining
Even the best programming and tools can’t produce quality parts if the material isn’t held securely. Poor fixturing causes movement during custom CNC machining, leading to dimensional errors and scrapped parts.
Use Precision Fixtures
Fixtures (jigs, clamps, vises) must hold the material firmly without distorting it:
- Custom jigs: For complex parts, design jigs that match the part’s shape, ensuring consistent positioning across multiple custom CNC machining runs.
- Vacuum chucks: Ideal for thin materials (e.g., metal sheets) that might warp under clamp pressure.
- Soft jaws: Made from aluminum or plastic, these protect delicate surfaces (e.g., polished plastics) from clamp marks during custom CNC machining.
Always check fixturing before starting—gently tap the material to ensure it doesn’t shift. Use indicators to verify alignment with the machine’s axis, ensuring the part is centered correctly.
Minimize Setup Changes
Each time a part is repositioned (multiple setups), the risk of error increases. Design parts for single-setup custom CNC machining when possible. For multi-sided parts, use 4-axis or 5-axis machines to complete all operations in one run, reducing alignment mistakes.
Implement Strict Quality Control for Custom CNC Machining Parts
Quality control (QC) ensures custom CNC machining parts meet specifications before they’re shipped. A robust QC process catches errors early, reducing waste and rework.
In-Process Inspections
Check parts during custom CNC machining at critical stages:
- First article inspection: After programming, machine one part and inspect it thoroughly. Use calipers, micrometers, or coordinate measuring machines (CMMs) to verify dimensions against drawings.
- Mid-run checks: For large batches, inspect every 10–20 parts to catch tool wear or fixture shifts before they affect multiple pieces.
Digital tools like laser scanners can quickly compare parts to 3D models, highlighting deviations as small as 0.0005 inches.
Final Inspections
After custom CNC machining, perform a full inspection:
- Dimensional accuracy: Use CMMs for complex parts to measure all features, ensuring they match CAD drawings.
- Surface finish: Check for roughness, scratches, or burrs using a surface profilometer. Parts like gears or bearings need smooth finishes to function properly.
- Functionality: For critical parts, test performance (e.g., load testing for structural components) to ensure they work as intended.
Document all inspections with reports, providing customers with proof of quality for their custom CNC machining parts.
Train Operators and Follow Best Practices for Custom CNC Machining
Even the best equipment can’t produce quality parts without skilled operators. Proper training and standardized processes are key to consistent custom CNC machining results.
Operator Training
Ensure operators understand:
- Machine setup: How to load materials, align fixtures, and calibrate tools.
- G-code basics: How to read and modify programs to fix minor errors.
- Troubleshooting: Identifying issues like tool wear, vibration, or material defects during custom CNC machining.
Certifications (e.g., NIMS, FANUC) validate operator skills, ensuring they can handle complex custom CNC machining tasks.
Standardize Processes
Create written procedures for:
- Machine startup/shutdown: Including warm-up times for CNC machines to ensure thermal stability.
- Tool change intervals: Based on material and cut type (e.g., replace carbide end mills after 500 inches of aluminum cuts).
- Cleaning: Regularly remove chips, coolant, and debris from machines and tools to prevent contamination.
Standardization reduces variability, ensuring every custom CNC machining run produces parts of the same quality.
FAQ: Custom CNC Machining Parts
What is custom CNC machining?
Custom CNC machining is a manufacturing process where computer-controlled machines cut, shape, or drill materials (metals, plastics) to create unique parts based on specific designs or drawings.
What tolerances can custom CNC machining achieve?
Modern CNC machines can hold tolerances as tight as ±0.0001 inches, though typical tolerances for most parts are ±0.001–±0.005 inches. Tighter tolerances require more precise equipment and slower machining.
How do I choose between 3-axis and 5-axis CNC machining?
Use 3-axis machines for simple, flat, or basic 3D parts. 5-axis machines are better for complex parts with angles, curves, or multiple sides, as they reduce setup time and improve accuracy.
Why do custom CNC machining parts sometimes have rough surfaces?
Rough surfaces are often caused by dull tools, high feed rates, or machine vibration. Using sharp carbide tools, optimizing speeds/feeds, and securing the machine to a rigid foundation can fix this.
How long does it take to produce custom CNC machining parts?
Simple parts (e.g., brackets) can be machined in minutes, while complex parts (e.g., aerospace components) may take hours. Batch size, material, and part complexity affect lead times.
Can custom CNC machining handle large parts?
Yes, large-format CNC machines can handle parts up to several feet in size (e.g., industrial machine frames). These machines use heavy-duty spindles and rails to maintain accuracy.
Table of Contents
- How to Achieve High-Quality Custom CNC Machining Parts
- Start with Material Selection for Custom CNC Machining
- Invest in Quality Equipment and Tooling for Custom CNC Machining
- Optimize Programming for Custom CNC Machining
- Ensure Accurate Fixturing and Workholding in Custom CNC Machining
- Implement Strict Quality Control for Custom CNC Machining Parts
- Train Operators and Follow Best Practices for Custom CNC Machining
-
FAQ: Custom CNC Machining Parts
- What is custom CNC machining?
- What tolerances can custom CNC machining achieve?
- How do I choose between 3-axis and 5-axis CNC machining?
- Why do custom CNC machining parts sometimes have rough surfaces?
- How long does it take to produce custom CNC machining parts?
- Can custom CNC machining handle large parts?